your current location is:Home > Finance > depthHomedepth
4680 battery: Tesla fell into "mass production purgatory"?
"We will have mass production of 4680 cells by the end of the year, but it's hard to predict because there's a lot of new technology in there." At Tesla Inc's 2022 shareholder meeting in early August, the company's CEO Elon Musk said, "We are confident that we will have high production rates, but we may not be able to achieve high production until the end of this year."
But when he said this, Musk's voice was not very confident. Musk, who was dressed in black, held the microphone, his face was a little dignified, and his eyes fell to the ground twice. Compared with the high-spiritedness of two years ago, it seems to be different.
In September 2020, on Tesla's "Battery Day", Musk launched the "epoch-making" Tesla 4680 battery. According to his statement, this battery will achieve a production capacity of 100GWh in 2022, which is at least 100 GWh. 10,000 electric vehicles to provide support.
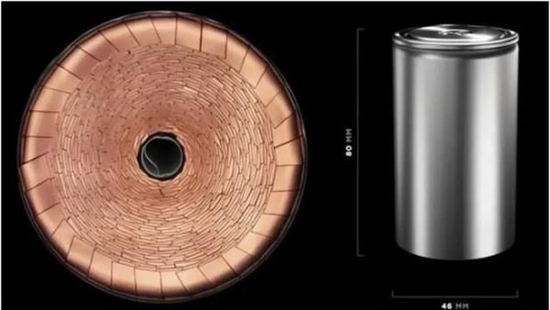
However, the reality is far from what Musk expected.
To date, Tesla has only started small-volume production of 4680 cells at its Kato Road plant near Fremont, California, and its Austin Gigafactory, Texas. One of Tesla's suppliers, the battery manufacturer Panasonic Corporation of Japan, made it clear that the 4680 battery is still in the testing stage, and mass production will not begin until April 2023.
Not only has Panasonic delayed the mass production plan, but also one of the rumored Chinese partners of the 4680 battery, Ningde Times New Energy Technology Co., Ltd., the relevant plans are still hazy. On August 17, when a reporter from The Paper asked the relevant person in charge of CATL about the company's progress in mass production of 4680 batteries, he said that CATL has no information about 4680 batteries to disclose.
What happened to the 4680 battery?
The full name of the 4680 cylindrical battery is the 4680 specification electrodeless (all-pole) cylindrical battery. 4680 refers to the size of the battery - 46 refers to a cylindrical battery with a diameter of 46mm, and 80 refers to a battery with a height of 80mm.
According to the data released by Tesla, compared with the traditional 2170 cylindrical battery, the energy of the 4680 battery will be 5 times that of the former, the cruising range of the vehicle will be increased by 16%, and the power will be increased by 6 times. Improvements, the net increase in range will be as high as 56%, and production costs can be saved by 54%.
Tesla's Kato Road factory near Fremont, California, was originally a small pilot plant, but now it has become the main production point for 4680 batteries. The 4680 battery production line of the Texas Gigafactory has only been put into production in small quantities since the second quarter of this year.
At the beginning of this year, the Kato Road factory produced the millionth 4680 battery. In April of this year, the first Tesla Model Y loaded with 4680 battery packs was assembled and delivered at the Texas Gigafactory, and the batteries used were also produced by the factory.
At present, there is no published battery output and capacity data from the Kato Road factory. However, from a document leaked from the Kato Road factory in the first half of this year, we can get a glimpse of the production efficiency of 4680 batteries at the factory. According to the autoevolution website, the leaked document shows that the factory had 14 machines running that day, of which 13 produced "good" quality batteries with a pass rate of over 90%, with one exception, machine 212 due to training Employees from the Gigafactory in Texas produced 82 percent of the "bad" batteries. According to statistics, the overall production pass rate of the battery that day was 92%.
In terms of output, the Kato Road factory produced a total of 6,250 4680 batteries that day, and a Tesla Model Y currently assembled at the Texas Gigafactory requires about 690 4680 batteries. According to the production of the Kato Road plant that day, the amount of batteries produced per day supports about 10 Model Ys, which is far below the target output of the Texas Gigafactory.
Production efficiency and capacity are still slowly climbing. According to Troy Teslike, an analyst who has followed Tesla for a long time, production efficiency at the Kato Road plant will increase in August, with 220 battery packs per week, while the Gigafactory in Texas will produce 220 battery packs per week. 183 battery packs were produced. However, Tesla won't reach weekly production of 5,000 4680 battery packs until May 2023.
According to a report on the insideevs website, in late July, Andrew Baglino, Tesla’s senior vice president of powertrain and energy engineering, said on an investor conference call, “Tesla wants a battery factory in Austin. By the end of 2022, it can surpass the weekly production of the Kato Road factory, which is expected to produce more than 1,000 battery packs per week by the end of the year.”
The Paper reporter learned that, according to Tesla's plan, the annual production capacity of 4680 batteries at the Kato Road factory will reach 10GWh, which can probably meet the needs of 150,000 electric vehicles; the production capacity of the Texas Gigafactory is expected to be built within this year. 60GWh. At present, Tesla's own 4680 battery capacity under construction also includes Tesla's Berlin plant, which is expected to reach 20GWh after completion, but the production capacity will not be released until the fourth quarter of 2022.
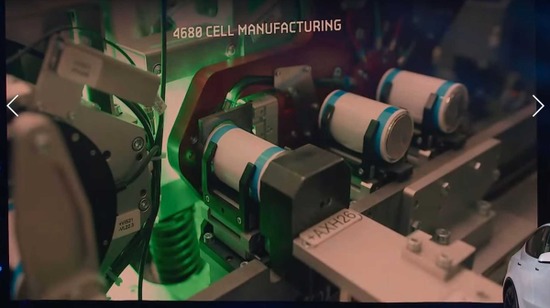
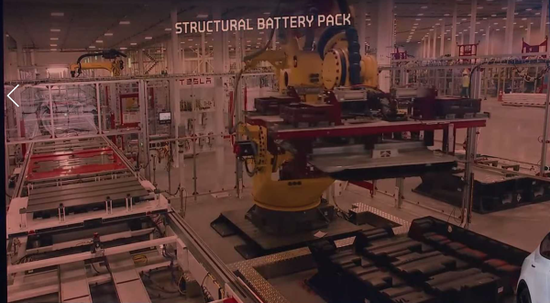
In terms of partners, Japan's Panasonic and South Korea's LG New Energy have both expressed their capacity plans for 4680 batteries. However, Panasonic has made it clear that the current 4680 battery is still in the testing stage, and the company will gradually expand its production capacity to prepare for comprehensive promotion. It is understood that Panasonic's Wakayama plant in western Japan is building two new production lines this year with a capacity of about 10 GWh. In fiscal year 2023 (April 2023-March 2024), the factory will begin mass production of 4680 cells.
South Korea's LG New Energy announced in June that it would invest 580 billion won (about 3.8 billion yuan) to build a new 4680 battery production line at the second factory in Wuchang, Chungbuk, South Korea, to supply Tesla with a production capacity of 9 GWh, but the time to put into mass production is also in the second half of next year.
Kazuo Tadanobu, CEO of Panasonic's energy division, previously told Bloomberg News that the 4680 battery has the potential to drive significant progress in the auto industry by reducing the cost of electric vehicles while maintaining safety and improving performance. . However, so far, the process has not been easy.
"It's not just about making a bigger battery. The work is not as easy as some people think," said Kazuo Tadanobu. "Panasonic has been experimenting with this for over a year." He said the battery development process " It takes a lot of stamina" and changing the shape of the battery requires "considerable brain circuits".
What are the difficulties in mass production of 4680 batteries?
In theory, cylindrical batteries have the highest technological maturity. In the early stage of Tesla, Panasonic's 1865 cylindrical battery products were widely used, but for electric vehicles, 1865 cells have a small capacity (generally no more than 3.5Ah) and a large number of cells (6000- 7000), the battery management is difficult. As a result, Tesla and Panasonic further launched the 2170 cylindrical product. The larger volume can accommodate more electrode material and save the space of structural parts. Compared with 1865, 2170 has a certain improvement, but there is no qualitative leap. It can only be regarded as a fat version of 1865.
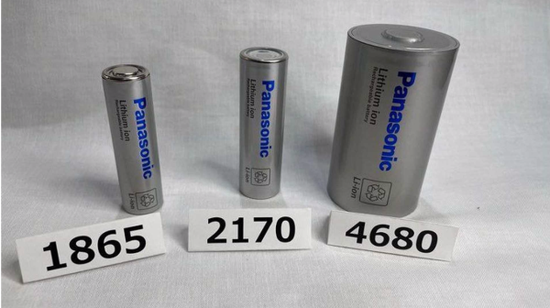
In the eyes of industry insiders, compared with 1865 and 2170 batteries, the mass production of 4680 batteries is very difficult, because it is indeed a fusion of multiple innovative technologies.
First, it requires higher precision for the battery winder, and alignment is more difficult due to the larger size of the battery. The main difficulty also exists in the welding process of the tabs. Among the 4680 batteries Tesla is most proud of is the battery's poleless (full pole) technology. The tab of the battery cell refers to the metal conductor that leads the positive and negative electrodes from the battery cell, and is the key path when the battery is charged and discharged. The material and size of the tabs will affect the internal resistance and overcurrent capability of the cell.
The traditional 18650 cylindrical product usually has only two tabs, which are connected to the positive and negative poles respectively due to their small capacity and low output current (as shown on the left side of the figure below). The 4680 cylinder uses an all-tab design, and the positive aluminum foil and negative copper foil exposed from both ends of the winding body are rolled into one end face as a tab (as shown on the right side of the figure below). The number of tabs increases, and the current paths also increase. At the same time, the distance between the tabs can also be shortened, thereby greatly reducing the internal resistance of the cell, effectively reducing the heat generation of the cell, and increasing the energy of the fast charging and discharging of the cell.
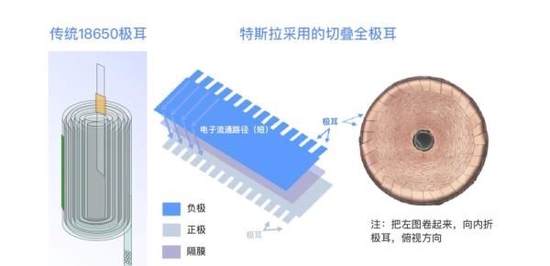
At present, there are two kinds of production processes of the full pole ear: the cutting and stacking method and the kneading and flattening method. The cutting and stacking method is a solution adopted by Tesla. It is mainly rolled up by obliquely cutting the sheet, and the surface has large fluctuations, which is likely to cause inconsistent contact between the tabs and poor consistency of internal resistance.
In addition, when the electrolyte is injected, since both ends are closed by the tabs, continuous injection production cannot be performed. The flattening method is a scheme widely used by domestic companies in China, which uses ultrasonic waves or mechanical friction to rub the tabs into end faces. During the flattening process of the tabs, metal debris is likely to be generated, resulting in excessive self-discharge of the cell, or even an internal short circuit. In addition, the rear end surface of the kneading flat is relatively dense, and it is difficult for the electrolyte to enter the interior of the cell. These will become a difficult problem to improve battery productivity.
Second, the space utilization of the battery is low. Under the same chemical system, the space utilization of large cylindrical cells is much lower than that of prismatic cells. If a ternary material is used, the prismatic battery can use ordinary nickel-cobalt-manganese (532) or nickel-cobalt-manganese (622) material, but the 4680 battery must use high nickel to have similar power, and its nickel-cobalt-manganese content ratio is currently about "811". Although high-nickel ternary compounds have higher energy density, they also mean a higher risk of thermal runaway, which must be paid attention to at the system protection level.
Third, the traditional method is difficult to dissipate heat. Most of the heat generated by the battery comes from the electrochemistry itself. The cylindrical battery generally dissipates the fastest axial heat and the slowest lateral heat dissipation. The large volume of the 4680 battery makes this feature more obvious. Under 800V high-voltage charging, the battery will accumulate a lot of heat in a short period of time, and the side heat dissipation speed will be slower. In the long run, it will have a bigger impact on the life of the battery. The way Tesla uses is to add a water-cooling plate on the top to achieve the effect of two-way cooling on the side and the top. It is currently unknown how the effect will be.
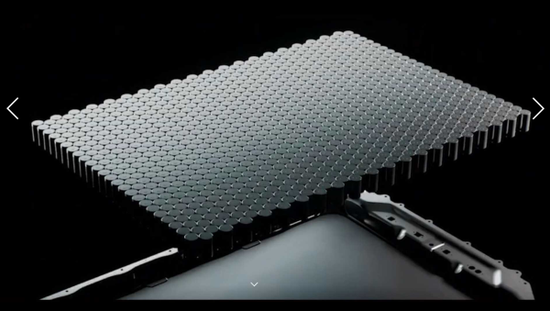
Fourth, the negative electrode material is insufficient. The anode of the 4680 battery is planned to use silicon carbide to improve energy density. However, silicon carbon anodes also have some disadvantages. For example, the cost is very high; there are many side reactions, large expansion, low efficiency of one charge and discharge, which affects the quality of the battery; the battery is easily affected by the change of silicon volume. The SEI film (solid electrolyte interface film) is repeatedly destroyed and remodeled, and lithium ions are consumed in large quantities, which may degrade the cycle characteristics and battery capacity.
However, it is quite mysterious that in early August, according to The Limiting Factor, a technology channel that has long been concerned about electric vehicle batteries, the 4680 battery was disassembled and chemically analyzed. The results show that the negative electrode of the 4680 battery that has been produced is only composed of graphite. , and does not contain silicon material.
Maybe a little patience
Tesla had to continue to rely on 2170 cells produced at its Texas Gigafactory to meet demand for the Model Y due to the production hurdle of 4680 cells.
"We have enough 2170 batteries to meet the rest of the new car needs this year. Tesla doesn't need to rely on 4680 batteries this year, but 4680 batteries will play a very important role next year." At the shareholder meeting, Musk said. The mass production schedule of the 4680 battery may not affect Tesla's goal of producing 1.5 million new cars this year, but 2023 will be different.
Because it is critical to the smooth mass production of Tesla's electric pickup, the Cybertruck. When launching the Cybertruck, Tesla promised a series of excellent performances, and the 4680 battery was necessary to deliver on those promises. Industry insiders believe that the mass production of Tesla's 4680 is far behind the original plan, which directly affects the mass production of models such as the Cybertruck and the electric semi-truck Semi.
However, the good news is not without. The 4680 cells that have been produced still show advantages in terms of energy density and fast charging performance.
According to the dismantling test report of Tesla 4680 battery by The Limiting Factor, a 4680 battery weighs about 355g and has a total capacity of about 26.136Ah. According to the rated voltage of 3.7-3.8V, the rated energy is about 96-99Wh. Simple calculation, the current energy density of 4680 cells is about 272-296Wh/kg, and according to Tesla's iterative plan, the energy density of the second generation 4680 battery will reach 305 Wh/kg, and the third generation will reach 333 Wh/kg.

For comparison, the system energy density of BYD's first-generation blade battery is 140Wh/kg, and it is expected to be greater than 180Wh/kg in 2025. The system energy density of the latest Kirin battery ternary high nickel system of CATL is 255Wh/kg, and it can reach 160Wh/kg under the lithium iron phosphate system. In terms of energy density, 4680 batteries have certain advantages.
In addition, in April of this year, Tesla delivered a Model Y equipped with 4680 batteries produced at the Texas Gigafactory. The first customers to get a chance to drive the new model were pre-orders in the Austin area, and many provided a lot of information on mileage testing and charging testing of the 4680 battery.
In one test, the user charged the battery on a V3 Supercharger in Texas to 9% in 3 minutes, 9% to 50% in 12 minutes, 80% in 34 minutes, and 40% in 40 minutes. 90%, 97% in 50 minutes. However, the new battery can't sustain the 250kW top charge for very long, and the top value of the speed drops faster than the 2170 battery.
"In any case, it is still too early to make a proper evaluation of the 4680 battery." An industry insider commented.
Andrew Bagrino, Tesla's senior vice president of powertrain and energy engineering, stressed that Tesla's challenge with the 4680 battery is an engineering problem, not a scientific one. This means that with enough optimization work, Tesla may be able to get out of the 4680 battery mass production dilemma.
related articles
Article Comments (0)
- This article has not received comments yet, hurry up and grab the first frame~